MINERAL PROCESSING
Mineral processing is science and art of extracting metals and nonmetal from their ores, refining them and preparing them for use. Within extractive metallurgy, the major divisions in the order they may most commonly occur are, Mineral Processing (or Beneficiation),
In mineral processing, a number of unit operations are required to prepare and classify ores before the valuable constituents can be separated or concentrated and then forwarded on for use or further treatment. The field of mineral processing has also been given other titles such as mineral dressing, ore dressing, mineral extraction, mineral beneficiation, and mineral engineering. These terms are often used interchangeably.
Ores and Mineral
Ore is a term used to describe an aggregate of minerals from which a valuable constituent, especially a metal, can be profitably mined and extracted. Most rock deposits contain metals or minerals, but when the concentration of valuable minerals or metals is too low to justify mining, it is considered a waste or gangue material. Within an ore body, valuable minerals are surrounded by gangue and it is the primary function of mineral processing, to liberate and concentrate those valuable minerals.
MINERAL PROCESSING OF DHAUBADI IRON ORE
Department of Mines and Geology, under Ministry of Industry, Commerce and Supplies Government of Nepal has signed MOU with Southwestern Metallurgical Geological Testing Center under Sichuan Institute of Metallurgical Geology & Exploration (SIMGE) for mineral process and pilot test lab facilities for Dhaubadi Iron Ore.
A. First MOU, Metallurgical test, completed
1. MOU (dated 26 JUNE 2018) for Metallurgical and others different levels of testing of Iron ore was completed and final report are received as:
Result of Metallurgical test
- TFe content in ore content is 35.36%, the main impurity constituent is silica (SiO2) with content of 44.88%, the content of Al2O3, CaO, MgO, P and S is respectively 1.86%, 0.24%,0.19%, 0.04% and 0.02%.
- Combined magnetic separation is recommended which could obtain the qualified iron concentrate with the TFe content of 56.70% and recovery rate of 65.21%.
- Roasting of concentrate at 1200°C temperature for 60 minutes could get qualified sponge iron with the TFe content of 95.28% and recovery rate of 89.06%.
B. Second MOU, Pilot Test, on going
1. As continuity of Metallurgical test for MoU for pilot test of hematite was signed on 17th June, 2019. The main objective of the MoU were:
- To conduct pilot testing and develop process flow of hematite ore
- To ascertain iron recovery from the iron ore needed to conduct techno-economic feasibility study of iron plant; and
- Transfer technical knowledge through on the job training and exposure visit of related human resources of Department of Mines and Geology (DMG).
SAMPLE COLLECTION
About 5300 Kg hematite samples within 16 different places from Pokhari, Ramche and Dhaubadi blocks of Dhaubadi iron deposit, Nawalpur District in month of June, 2019.
PILOT TESTING
- 5 ton of sample collected from 3 different blocks of Dhaubadi iron (Pokhari, Ramche and Dhaubadi Blocks) was sent to SIGME
- SIGME received samples on 2 September 2019 and carried out the related research work with a focus on improving the TFe grade and reducing the silicon in concentrate
B. Second MOU, Pilot Test, on going
- Samples from each three block were mixed, crushed and analyzed
Sample Packed
Crushed Sample in SMGTC
Chemical Analysis of Sample
The analysis results indicate that, the Fe in the ore is the main recovery composition with content of 34.84%; the main impurity composition is SiO2 with content of 44.70%; the content of K2O, Na2O, P and S is respectively 0.012%, 0.013%, 0.034% and 0.003%.
Name | Weight | Product Rate | TFe Grade |
---|---|---|---|
Pokhari | 1549.00 | 30.98 | 34.65 |
Namche | 2516.00 | 50.32 | 32.36 |
Dhaubadi | 935.00 | 18.70 | 39.30 |
Total | 5000.00 | 100.00 | 34.37 |
Objective of Pilot Test
The main objective of pilot test is get qualified concentrate from low TFe grade hematite ore. previous.
Sample Preparation of Pilot Test
Jaw Crusher and roll crusher are used for grinding samples to the size of 3 mm which was completed.
Ore Characteristics and Mineral Composition
- Process mineralogy characteristics of this hematite ore showed that the total iron grade was 34.84%, mainly existing in the form of hematite and goethite
- Other minerals are mainly quartz and chlorite. Iron minerals mainly exist in the form of fine hematite and is observed as oolitic.
- The structure of the ore has an important influence on the mineral processing process.
.jpg)
.jpg)
.jpg)
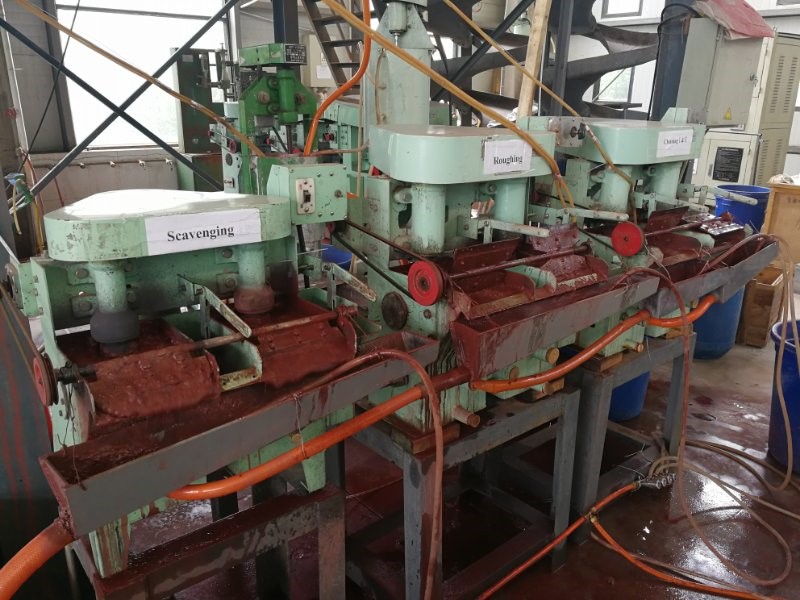
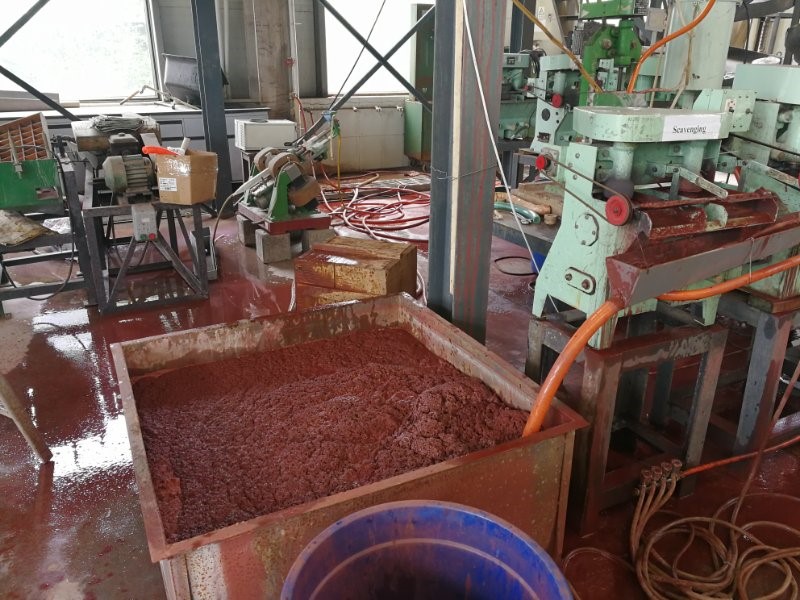
RESULT OF PILOT TEST
Raw Ore—Crush and Grinding—Magnetic Separation—Grinding—Reverse Flotation—Concentrate.
- The recovery of rough concentrate in magnetic separation is 86.53%
- The recovery of concentrate in flotation is 80.92%
- Final recovery of concentrate is 70.02% with Tfe 56.94%
SIGME recommended Magnetic Separation- Reverse Floatation which could obtain qualified concentrate with TFe 56.94% in recovery rate of 70.02%.